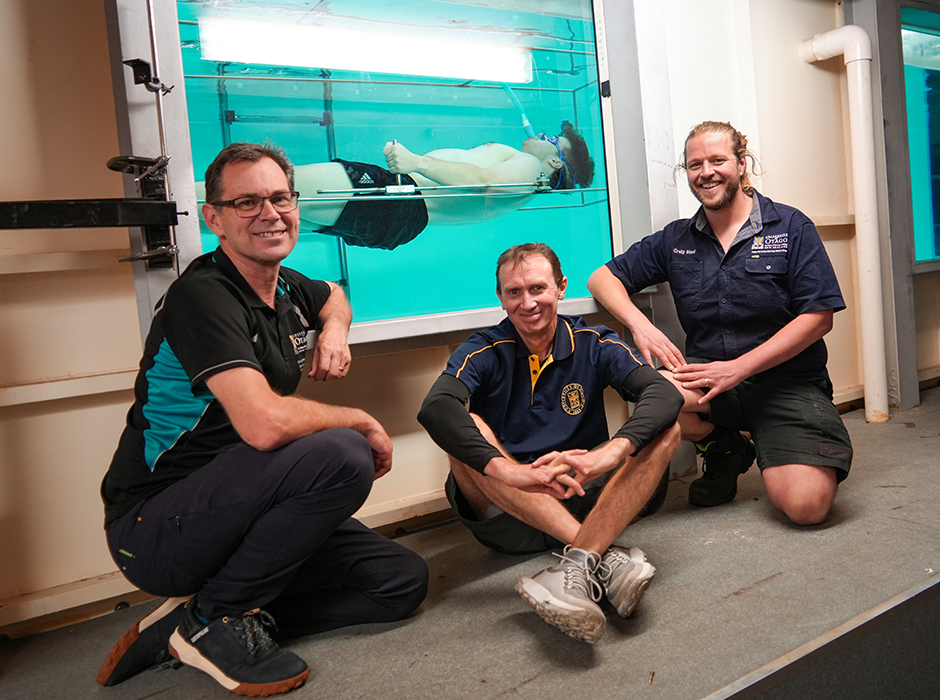
From left: Nigel Barrett, Chris Button and Craig Steel, with the weighing frame in the background.
If you’re looking to custom-build something, Craig Steel is the one to call.
While Property and Campus Development Leading Hand Engineer Craig started his career as a sheetmetal engineer, these days he’s a deft hand at turning specifications and drawings into bespoke equipment.
Craig, who has been with Otago for eight years now, started out working on ducting and ventilation installs for lab fitouts.
His shift from sheetmetal ducting to “odd jobs” was “an accident, literally”, Craig says.
“After the first Covid lockdown, I had a fall off a Lime scooter and tore a tendon in my shoulder.
“This restricted me to light duty with no overhead lifting, and so I started exploring other odd jobs I could do while I healed.”
This meant learning how to do new things and his skills have grown since he started, Craig says.
“I’ve learned how to do machining on a lathe and my welding has come a long way.”
Some of his projects have included building a customised base for a racing simulator for high performance motorsport research, a customised helmet to attach to a Biodex System for neck muscle strength testing and a trolley fitted with a 360-degree camera for use in livestreaming surgeries for teaching purposes.
“Simple yet effective” is Craig’s approach when it comes to figuring out how to build customised equipment.
“It's all about going through the process of what we can do versus what we can’t and combining that with what's going to get the desired outcomes.”
From design to build can take anywhere from a couple of days to a few weeks, Craig says.
“The Biodex helmet, for example, was a pretty tricky one.
“We were trying to replicate the helmet off images from a previous paper and the images didn’t show much detail, especially with how the helmet connected to the Biodex and how it was adjusted to account for participant’s different heights.
“I spent about two weeks figuring it out and building the helmet.”
It’s the “problem-solving and the thinking outside the box” that draws Craig to building bespoke equipment.
“While our team does a lot of regular maintenance too, it’s the odd tasks that make my job really interesting.”
He is now one of the go-to guys for “by request” work across the Dunedin campus.
“We do all sorts of odds and sods all over campus. If someone wants something done, we can figure out how to make it.”
Craig’s latest project involved building a frame to weigh people underwater for research in the School of Physical Education, Sport & Exercise Sciences (SPESES) Te Kura Para-Whakawai.
SPESES Professor Chris Button is lead researcher for the project using the frame, which aims to measure participants’ centre of buoyancy and determine why there are individual differences in floating.
The use of a horizontal frame is novel, having been used only once before in a study done in the 1990s, Chris says.
“Historically, when people have been weighed underwater, it’s done in a seated, vertical position. But this can be difficult for participants and the variables require researchers to make multiple measurements to get an average.”
By lying face-up in a horizontal frame with a snorkel for breathing, participants are more relaxed, Chris says.
“The horizontal position also allows us to measure a participant’s weight from two points, which is required to measure buoyancy.”
And while there are alternate ways to measure buoyancy, such as full body X-ray scans, the weighing frame generates another set of data to factor in, Chris says.
“The frame that Craig built for us has been absolutely crucial in helping us collect these sensitive measurements.”
About 180 participants have been weighed in the frame to date, with a target sample of 200.
It was important the frame be built so it could be adjusted easily to accommodate participants’ heights and moved around easily for the research team to use, Chris says.
“Craig helped us tick all the boxes on this front. I am very grateful for the work he has done with us.
“Having this expertise in-house has been fantastic and we’re looking forward to working with Craig again.”
SPESES Technical Leader and Electronics Technician Nigel Barrett is the liaison between the School’s researchers and Craig’s team.
“We’ve found it’s hard to find someone with the right mix of vision, skill and creativity to build the equipment we’ve required.
“That’s where Craig is great. He’s terrific at combining a researcher’s outcome requirements with what will work mechanically.”
Understanding the researchers’ outcomes is the first step to working out the equipment required, Nigel says.
“These are not products you can buy off the shelf.
“Depending on the researcher’s requirements, a brief can take the shape of building equipment from scratch or modifying an existing piece to measure something specific.”
Having an in-house person to help with these requests makes the turnaround faster and more cost-efficient, Nigel says.
“The more Craig works with us, the easier and quicker we get our requirements sorted.
“Craig also has a broad range of skills and can do it all, which is a huge advantage for us,” Nigel says.
“It saves us from having to speak to multiple people, which is often the case when you work with external consultants.”
Craig’s precision-driven attitude definitely helps, Nigel says.
“Craig is very detail orientated and takes pride in his work. He will go the extra mile to make sure what he hands over is up to, or even above, standard.”
This is critical for SPESES research, where most of the research participants are external, coming on to campus, Nigel says.
“It is very important for all our equipment to look professional and function to research and health and safety standards. Craig gets that, which is why he is invaluable to us.”
~ Kōrero by Sandra French, Adviser, Internal Communications.