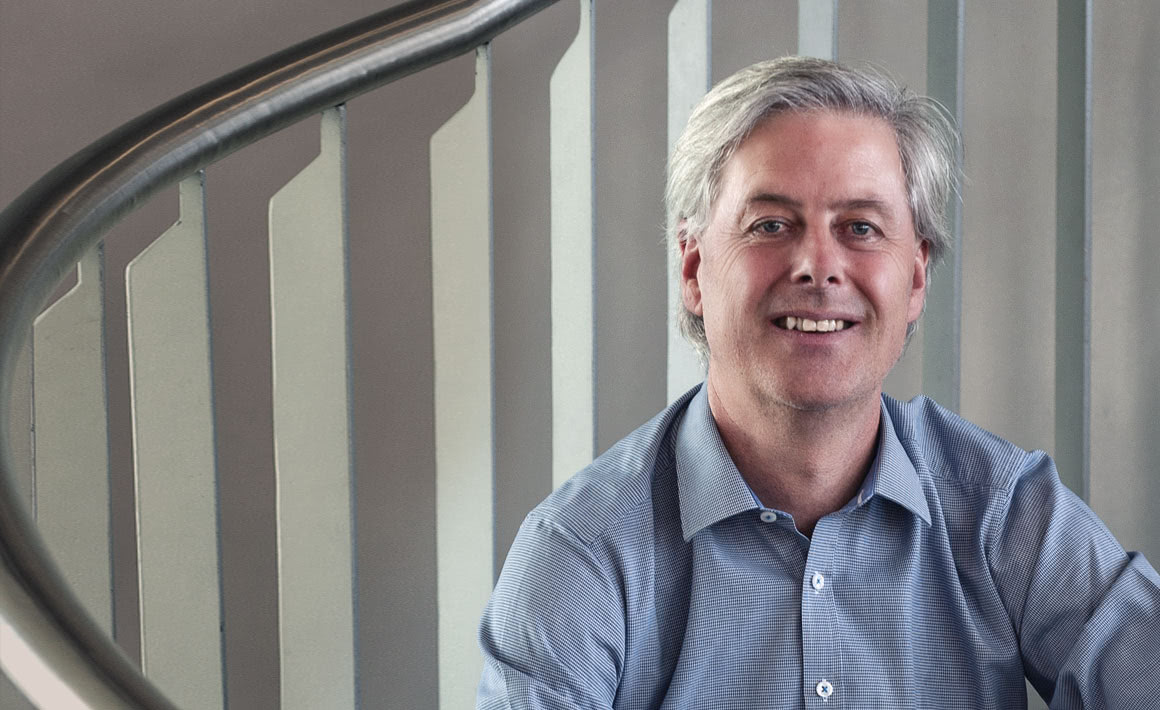
Otago scientists have responded to a call to action from the Ministry of Health to boost supplies of COVID-19 testing systems should global supplies run short.
The Diagnostics Development Working Group (C-19-DDWG) has been working since late March across New Zealand universities and government agencies, and is chaired by Otago's Deputy Vice-Chancellor (Research and Enterprise), Professor Richard Blaikie.
“Our aim is to gain self-sufficiency on COVID-19 testing as insurance against global shortages, to save money for the Ministry of Health, and to stimulate new export business opportunities.”
All aspects of testing are being investigated. “We have swabs in late-stage prototype form, and have identified home-grown sources for all the chemicals and reagents needed in molecular testing.
“Some of the work has already led to the production of control materials for use in diagnostic labs and new ways of extracting RNA from samples as part of the testing process. A full test is being validated by teams at MPI and ESR, and could be in wide use when approvals are gained and production is scaled up.”
“Similarly, home-grown antibody tests are showing promise, with results comparable to the best labs around the world.”
Blaikie says this work is a precursor to the contributions New Zealand can make to global vaccine and therapeutic developments, demonstrating capabilities for future manufacturing and supply.
Funding
Ministry of Health
Local production of swabs
Professor Raechel Laing: “Providing we could source the raw material, I believed we could work with a New Zealand company to manufacture for us here.”
As the COVID-19 virus began to spread in New Zealand it became clear that established international supply chains for nasopharyngeal swabs were no longer functioning. As testing needed to be rapidly increased, Otago's Professor Raechel Laing (Centre for Materials Science and Technology) set out to ensure some local supply.
“These swabs are made from fibres such as polypropylene or polyamide so, providing we could source the raw material, I believed we could work with a New Zealand company to manufacture for us here.”
Partnering with Zoomtech Ltd, a Dunedin-based company with capability in design, tooling and injection moulding of medical and agricultural devices, prototypes have now been developed and lab-tested by Associate Professor Jo Stanton, also a member of the C-19-DDWG.
Laing says the current prototype is injection-moulded in one piece. “The challenge was to ensure the structure of the tip is such that it collects sufficient material of interest, but also to ensure that the shank is sufficiently fine, flexible and resilient.” The project is progressing with the initial aim of producing 6,000 to 8,000 units per day.